Taking the pain out of medical device development and production
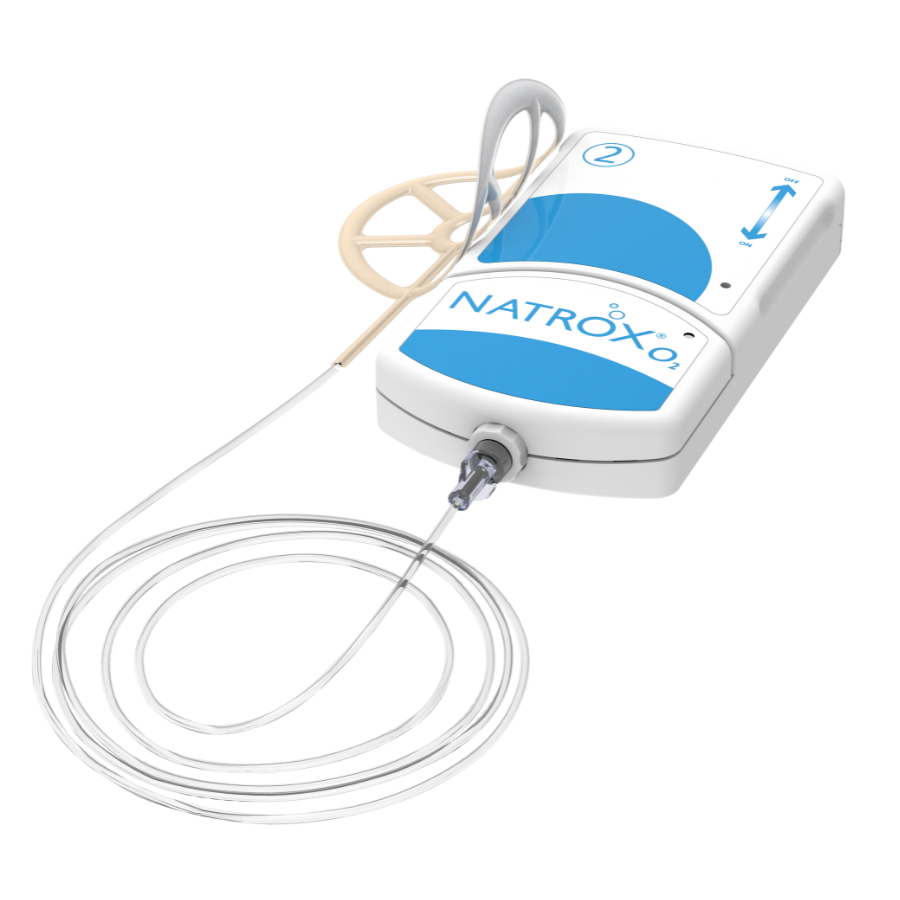
CASE STUDY
In this medical device case study, discover how Meridian Medical’s ability to adapt, innovate, and scale in response to a customer’s evolving needs contributed to the success of a groundbreaking wound care medical device.
The story of NATROX® O₂ is one of compassion and determination. Mel Vinton, the inventor of the technology, was driven by a deeply personal motivation – his ageing aunt’s unrelenting pain from a venous leg ulcer that refused to heal. Determined to alleviate her suffering, Mel embarked on a quest to understand wound healing. Through collaboration with friends at the University of Cambridge, Mel and his team developed what is now known as NATROX® O₂, an advanced topical oxygen therapy that harnesses the natural healing properties of oxygen to promote wound healing.
With a mission to share this groundbreaking solution and help patients worldwide, Mel and his team formed Inotec AMD Limited, a company focused on developing innovative medical technology.
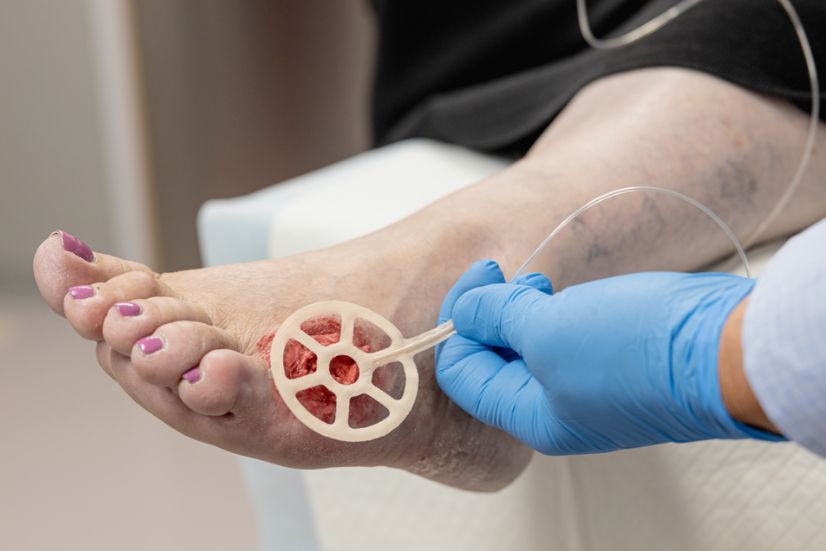
Design brief and initial production
Inotec AMD approached Meridian Medical in 2011 to produce the disposable aspects of the device. From the outset, Meridian Medical recognised the potential of NATROX® O₂ and committed to supporting its development, with the early stages of our collaboration laying the foundation for a partnership built on mutual trust and shared goals.
We established an initial production process using their RF tooling and our own small foot welding machine to produce the device, a process that worked well, but had limitations.
Inotec AMD challenged us to develop the device to a version with a longer tube, and then a fully certified cleanroom produced medical device, that could be CE certified and sold. We embraced this challenge, leveraging all our expertise and resources to refine and enhance the device.
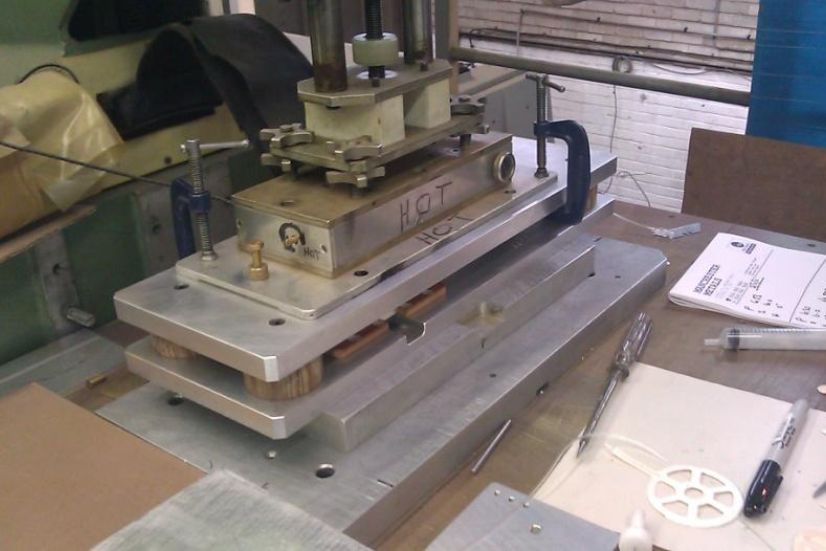
Using MK1 tooling, we produced a number of short cleanroom runs for initial feedback and some small clinical trial batches. Following those trials, we needed to redesign the device to increase the tube length. This increased the difficulty of the production, as the MK1 process uses a mandrel inside the tube to stop it welding shut during the processing of the dressing.
Working with our design team and toolmaker, we developed a process that would allow for any length of tube. Although this process change increased the production time, it allowed the welding process to be scaled from single impression tools to a multi-impression process.
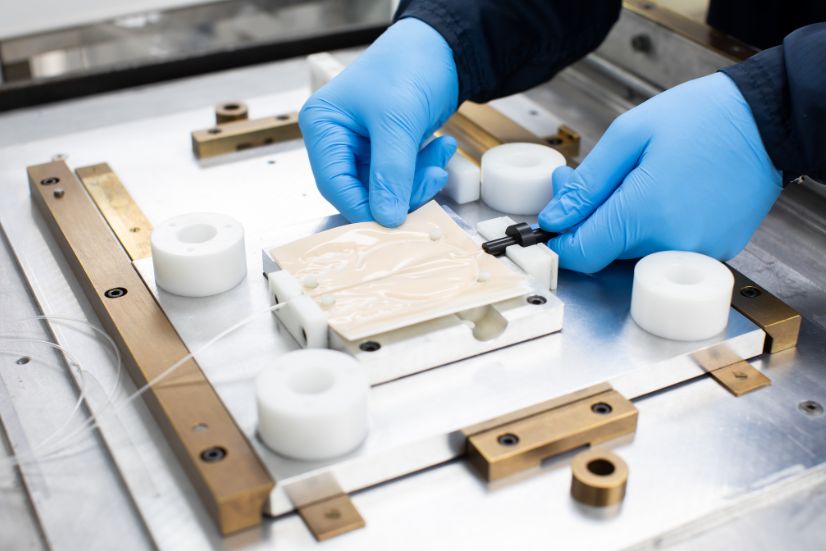
We then updated the process using the MK2 tool to enable any length of tube to be used, whilst allowing the device to be produced in a larger welding machine with a heated head and digital controls. This created a robust and repeatable process that could be validated for consistency and repeatable quality.
From concept to certified medical device
NATROX® O₂ hit the market and continued to be produced using the MK2 tooling. Its success in multiple countries led to a surge in demand in 2023, exceeding the output of the existing process.
Recognising the need to scale up production, Meridian Medical invested in a substantial upgrade to the process, including developing multi-impression tooling to increase output tenfold and building a new, dedicated cleanroom facility.
The MK2 tooling was scaled up to four impression tools mounted to two rotary welding machines, whose size prompted Meridian to build a brand new cleanroom to house the processing and create a dedicated production line for the device – a clear demonstration of our commitment to growing alongside our customers.
By January 2024, we had a fully validated production line capable of producing up to 16,000 units per week, with a team of skilled operators, quality controller and supervisor, ensuring quality and efficiency at every stage.
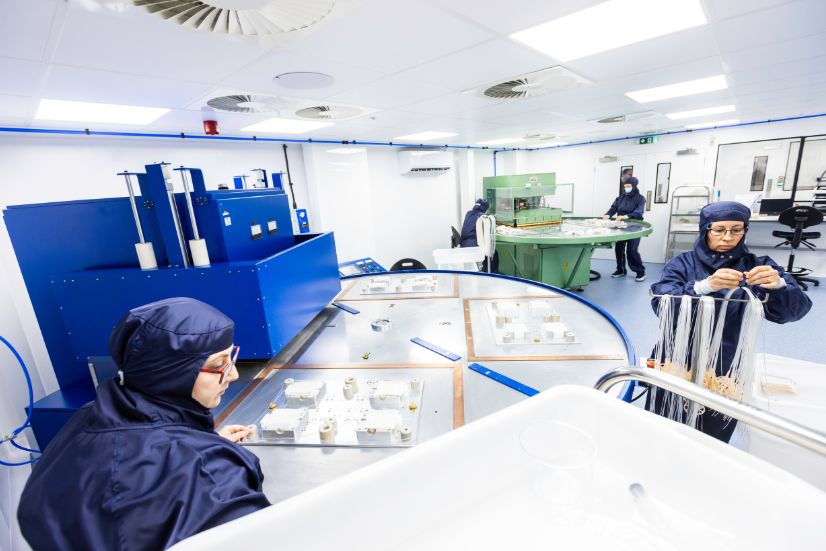
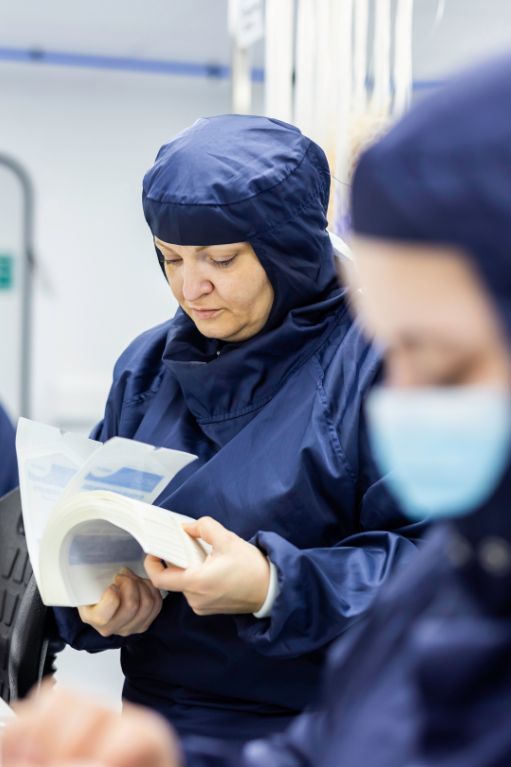
A relationship built on trust and shared success
The journey from a small-scale run to a dedicated high-volume production line illustrates the strength of the relationship between Meridian Medical and Inotec AMD. Our ability to adapt, innovate and scale in response to their evolving needs has supported the vision of NATROX® O₂.
John Adam, Inotec AMD’s Chief Operating Officer, has this to say about the company’s relationship with Meridian Medical: “The technical and product development between ourselves and Meridian has allowed us to better serve our patients by delivering innovative wound healing solutions around the world.”
This medical device case study showcases Meridian Medical’s commitment to fostering long-term relationships with our clients. By aligning our growth with that of our partners, we ensure mutual success and contribute to advancing medical technologies that improve patient outcomes.
For further details of the NATROX® O₂ medical device please visit the NATROX Wound Care website.
Please see the section on our website devoted to medical device contract manufacturing case studies, illustrating the strength of the relationships that we have with our clients and the ways in which we work with them to fulfil their contract manufacturing requirements.
Case study: Supporting in-house production
How Meridian Medical works as an extension of in-house manufacturing operations to extend a customer’s production capacity.
News: Medical device manufacturing and business news
Read insights and articles on issues affecting the manufacture of medical devices, covering an array of topics.