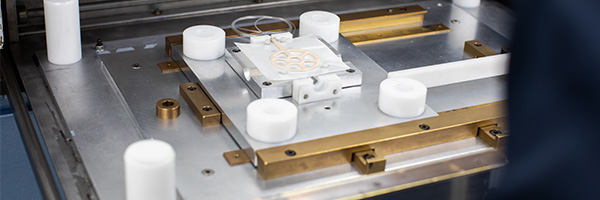
Radio frequency welding, or RF welding as it is more commonly known, is a key medical device manufacturing process. It has a direct impact on product and packaging quality and performance.
RF welding is the process of fusing materials together by applying radio frequency energy to the areas to be joined. This type of welding is widely used in medical device manufacturing because it is very cost-efficient and delivers a high level of consistency, helping to ensure that your medical products and packaging are safe, efficient and reliable.
Given the important role of RF welding, it is essential to be aware of what is involved in the process and to ensure that your medical device contract manufacturing partner has the capabilities and resources to deliver a consistently high-quality service.
What is RF welding and what it is used for?
RF welding uses heat and electromagnetic energy to permanently bond materials, creating a super-strong, airtight seal. The flexibility and speed of this process and the standard of the seal it provides help ensure that your medical products and/or packaging are of a consistently high quality.
This technology is used in the manufacturing of a wide range of medical devices and packaging, including:
- IV bags
- Waste collection bags
- Plasma bags
- Blood bags
- Drinks bags
- Oxygen bags
- Medical dressings
- Medical packaging pouches
What are the benefits of RF welding?
In the manufacture of many medical products, it is critical that air, moisture and other contaminants are kept out. The viability of your product and your brand reputation depend on achieving this.
There are a number of medical sealing methods available to manufacturers, including sewing, gluing and hot-air bonding, but RF welding is the most effective. One of the major advantages of RF welding is that it doesn’t require any consumables, which means it is a low-cost process.
Furthermore, because additional compounds, such as glue or thread, aren’t used in RF welding, biocompatibility isn’t an issue, which is helpful for meeting medical manufacturing regulations.
Compared to sewing, gluing and hot-air bonding, RF welding can be analysed as followed:
- In comparison with sewing, RF welding offers greater reliability and consistency in terms of the air- and liquid-tight seal it provides. A sewn seam is vulnerable to pressure and can break, while the nature of RF welding provides a much stronger, safer seal.
- The two main advantages of RF welding over gluing relate to the fact that gluing takes longer and can involve the use of toxic materials. RF welding is quicker and more environmentally friendly. Furthermore, it has greater longevity as the adhesiveness of glue can wear out.
- Hot-air bonding is only effective with materials up to a certain thickness. If the materials are too thick, hot-air bonding won’t form a reliable seal. RF welding works with materials of all thicknesses.
Medical RF welding – what you need to consider
When selecting a medical device contract manufacturer, it is important to consider the key processes involved in the manufacturing of your medical products and the resources and expertise that your prospective partner has at their disposal.
When it comes to RF welding consider the following:
- Does your prospective partner have the right expertise and experience?You should only trust the manufacture of your medical products to a specialist medical device contract manufacturer that has extensive expertise and experience in RF welding. Medical RF welding is a key manufacturing process and it is essential that it is carried out to the highest standard.
- Does your prospective partner have the necessary range of technology?RF welding requirements can vary for different applications and it is essential that your medical device contract manufacturing partner offers a range of RF welding machinery (e.g., from 4.5kw to 10kw). This will help ensure the efficiency of the manufacturing process and the quality of your products.
- Does your prospective partner have the proper RF welding facilities?The manufacture of medical products and packaging using RF welding must take place in a medical cleanroom. This guarantees that your products are suitable for medical use. As such, it is essential that your partner has the appropriate cleanroom facilities, certified to the necessary ISO standard.
Why it is key that your partner has advanced RF welding facilities
RF welding is a critical medical device manufacturing process and if the production of your medical product and/or packaging involves this technology, it is essential that you use the right contractor.
The standard of RF welding used in the manufacture of your product has a direct bearing on its quality and its suitability for use in a medical environment. This is why it is important to take the time to assess your partner’s RF welding expertise, experience and resources.
Meridian Medical is an established and experienced contract medical equipment manufacturer specialising in a wide range of medical device design, development and supply services.
To find out more about how Meridian Medical can help you with your medical product design and manufacture, get in touch today by filling out our online form or contacting us on 01903 732344 or info@meridian-medical.com.
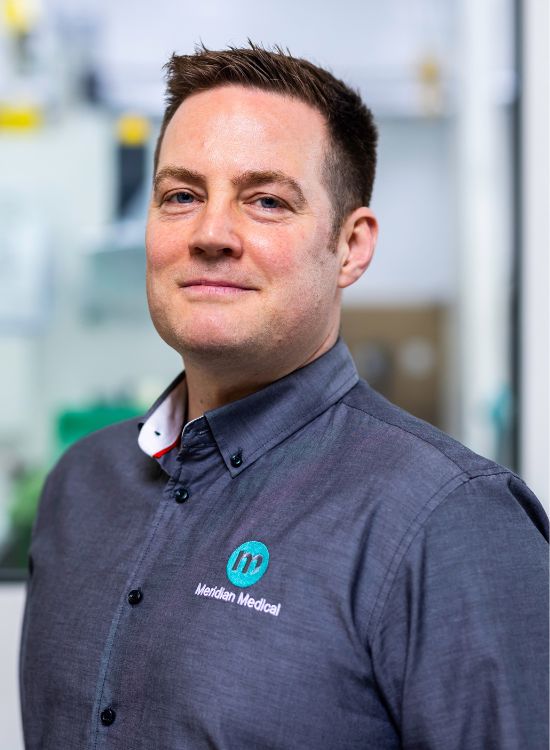
Author: James Fenton, Managing Director
James Fenton, Managing Director of Meridian Medical since 2017, has over 20 years of industry experience. He has been pivotal in developing and producing over 500 types of single-use medical devices, including CE-marked class 2 and 3 devices. With a strong focus on business strategy, project management and customer support, James ensures Meridian Medical's agility and innovation. His expertise is backed by qualifications in Business Studies and Medical Process and Equipment Validation, plus extensive industry training. James's insights into the industry that he has dedicated his entire career to provide a bank of invaluable information aimed at increasing knowledge of and driving advancements in medical device manufacturing.