Integrating Medical Device Design for Manufacturability: A Strategic Imperative for Meridian Medical
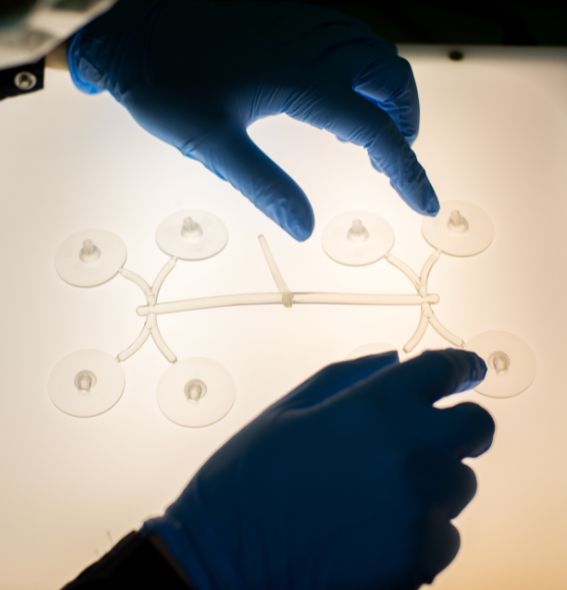
GUIDE
Within all industries and especially within medical device manufacturing, ensuring product quality, efficiency and cost-effectiveness is hugely important. One key approach to achieving these goals is being able to design products sympathetically to the production process. This is often referred to as Design for Manufacturability, or DFM for short. At Meridian Medical, integrating DFM principles into the entire design process is not just beneficial but imperative. In this article, we shall discuss the significance of DFM and why considering the method of production at all design stages is crucial for the success of your product.
Understanding Medical Device Design for Manufacturability
DFM is a proactive approach that focuses on optimising the design of a product for ease of manufacturing. It involves anticipating manufacturing challenges, streamlining processes and minimising complexities right from the conceptualisation phase. By prioritising medical device design for manufacturability, Meridian Medical can significantly reduce production costs, shorten time-to-market, enhance product quality and facilitate scalability.
Integral Role of DFM in the Design Process
Traditionally, designing medical devices has been treated as a separate entity from manufacturing, often resulting in costly redesigns and production delays. However, when your designer is sympathetic to the production process by understanding the strengths, weaknesses and limitations of a particular process that is expected to be used, the design process becomes cheaper and more streamlined. This integrated approach ensures that manufacturability considerations influence design decisions from the outset, rather than being an afterthought.
Key examples of medical device design for manufacturability
Here are some practical examples of product designs that Meridian Medical has received that have not been formulated for real-world manufacture.
1. The customer has 3D printed the prototype and is happy that it meets the specification. The CAD of a component has been sent over with the request for a quote for mould tools for injection moulding. The part has not been drafted and so cannot be ejected from tooling. The part needs a draft analysis performed and then the CAD updated and the design reviewed before it can be correctly quoted.
2. A component has been drawn with thick sections (typically thicker than 2mm) of plastic and has no coring out. The moulded part will be prone to have areas of sink, use excess plastic and will have filling issues. Additional time will need to be spent redesigning thick sections and to redesign the cored-out areas.
What five factors play a part in design for manufacturability?
There are five key principles when it comes to medical device design for manufacturability. These are:
1. Simplicity in Design: Complex designs often lead to intricate manufacturing processes, increasing the likelihood of errors, scrap and inefficiencies. By prioritising simplicity, you can minimise production complexities, reduce material waste and enhance overall reliability.
2. Material Selection: Optimal material selection is crucial for both functionality and manufacturability. By choosing materials that are readily available, cost-effective and compatible with manufacturing processes, you can streamline production and enhance product performance.
3. Standardisation: Standardising components and processes wherever possible can significantly simplify manufacturing operations. This not only reduces production variability but also enables economies of scale, driving down costs and improving consistency.
4. Design for Assembly (DFA): DFA focuses on designing components in a way that facilitates easy and efficient assembly. By considering assembly requirements during the design phase, we can minimise assembly time, eliminate potential errors and enhance overall productivity.
5. Design for Testing and Quality Assurance: Building testing and quality assurance mechanisms into the design ensures that product quality is maintained throughout the manufacturing process. By designing for testability, we can identify and address potential defects early, minimising rework and enhancing customer satisfaction.
Continuous Improvement and Feedback Loop
Medical device design for manufacturability is not a one-time effort, but rather a continuous journey of improvement. By soliciting feedback from manufacturing teams, analysing production data, and refining design iterations, we can enhance our DFM practices over time. This iterative approach enables us to adapt to changing market dynamics, technological advancements and customer preferences, ensuring that products remain competitive and relevant.
Driving innovation and improving patient outcomes
At Meridian Medical embracing medical device design manufacturing is not just about optimising production processes; it’s about driving innovation, enhancing product quality and, ultimately, improving patient outcomes. By making DFM integral to our design process and considering the method of production at all stages, we position ourselves for long-term success in the dynamic and demanding landscape of medical device manufacturing.
To find out more about how Meridian Medical can help you with your medical device manufacture, get in touch today by filling out our online form or contacting us on 01903 732344 or info@meridian-medical.com.
Case study: Supporting in-house production
How Meridian Medical works as an extension of in-house manufacturing operations to extend a customer’s production capacity.
News: Medical device manufacturing and business news
Read insights and articles on issues affecting the manufacture of medical devices, covering an array of topics.