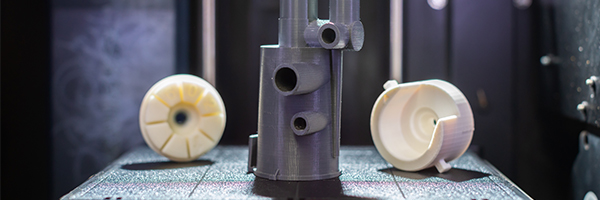
Medical product prototyping can be one of the most important stages in the medical device manufacturing process. The application of the right expertise and technology at the prototyping stage of manufacturing helps optimise the production process and plays a key role in ensuring the success of your medical device.
Why prototyping is integral to the performance of your medical device
When you outsource the production of your medical device, you need to know that the contract medical device manufacturer you choose has expertise in every area of the production process. The ability to produce working prototypes or pre-production samples is particularly important.
Prototyping knowhow has a broad scope: it ranges from the ability to make mock versions of a device using custom-made parts to the use of low-cost prototype injection-mould tooling. At Meridian Medical, our expertise spans this spectrum of services.
This prototype modelling expertise gives you a level of flexibility in terms of how you test, refine and develop your device that gives you a better product that gets to market quicker.
The prototyping services that your contract manufacturer should offer
To help you make the right decision for your product, here is what you should expect in terms of medical device prototype services from your contract manufacturer.
Your contract medical devices manufacturer should:
- Have advanced design capability – this means having the in-house expertise to review and understand 2D sketches or ideas and, if required, create the 3D CAD data necessary for the next stage of the prototyping process. They should also be able to produce 3D CAD modelling that is suitable for using for the intended manufacturing technique.
- Use advanced 3D printing technology – such as fused definition modelling (FDM) technology. FDM technology creates strong, durable and dimensionally stable parts and boasts a very high level of accuracy and repeatability. Meridian Medical uses the latest model in the FDM range (the F170 model in the F123 series) from leading 3D printing system manufacturer Stratasys.
- Understand the device and its final application – this can significantly reduce the amount of prototype revisions and material changes required during the device lifecycle. This manufacturing-process experience and understanding can save you time and money.
- Have dedicated machinery for R&D and prototyping – using smaller machines that are not in constant use for production purposes can allow engineers time to refine prototype devices and quickly create mock devices without waiting for production slots.
- Have the capacity to create different types of prototype devices – the contract medical devices manufacturer you choose should be able to quickly and cost effectively create a wide range of device prototypes to a near-production-ready level of finish. Such devices include IV bags, pump sets, injection-moulded parts, radio-frequency welded assemblies and products for R&D testing.
Prototype modelling expertise is critical to the medical device manufacturing process and the quality of your product. For this reason, you should only use a contract manufacturer of medical devices that offers this knowhow as part of its end-to-end development and production service.
Meridian Medical is an established and experienced contract medical equipment manufacturer, specialising in a wide range of medical device design, development and supply services.
To find out more about how Meridian Medical can help you with your medical product design and manufacture, get in touch today by filling out our online form, calling us on 01903 732344 or emailing info@meridian-medical.com.
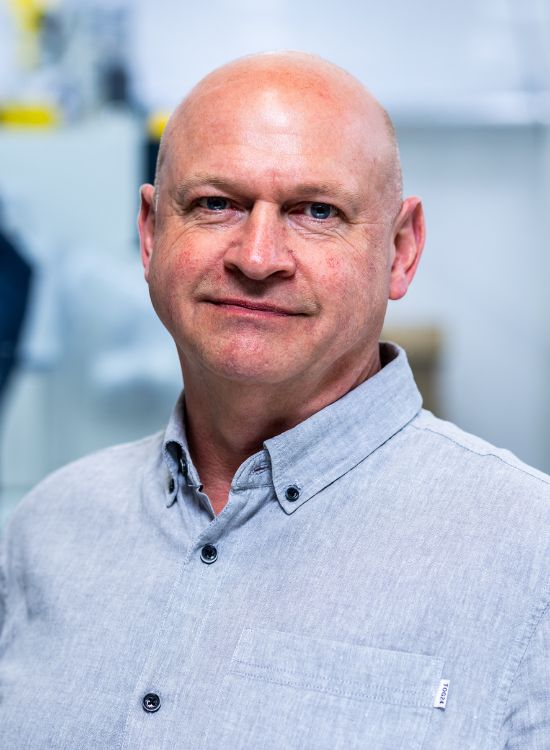
Author: Paul Kearsley,
Technical Manager, Meridian Medical
Paul Kearsley brings a lifetime of engineering expertise to his role as Technical Manager at Meridian Medical. With an HNC in Mechanical Engineering and a foundation built during a four-year engineering apprenticeship, Paul has spent over 40 years running his own design company. Over the decades, he has designed more than 1,000 consumer, industrial, and medical devices, showcasing his ability to deliver innovative solutions across a broad spectrum of industries.
A pioneer in the transition from traditional drafting techniques to modern CAD workflows, Paul began his career on the drawing board, adopted AutoCAD 2D early on, and embraced 3D modelling with SolidWorks in 1997. His vast experience and technical leadership play a key role in Meridian Medical’s commitment to producing high-quality, single-use medical devices.