Medical Device Technical File Requirements: Your Essential Guide
A medical device technical file is a crucial document that outlines all essential information about a medical device, ensuring its safety, performance and compliance with regulatory requirements. This guide covers the medical device technical file requirements, providing an overview of the key elements, regulatory requirements and best practices for creating and maintaining a technical file.
Whether you’re seeking regulatory approval or simply ensuring ongoing compliance, understanding the structure and contents of a medical device technical file is critical for success in the global market. This resource will help you to navigate the complexities of medical device regulations, from FDA submissions to EU MDR compliance*.
What is a Medical Device Technical File?
A medical device technical file is a comprehensive document that contains all essential information about a medical device, demonstrating its safety, performance and compliance with applicable regulations. It includes details such as the device’s design, intended use, manufacturing processes, risk assessment and clinical data.
Technical files are crucial for obtaining regulatory approvals, such as CE marking in the EU, ensuring the device meets legal standards for market entry. By providing clear evidence of compliance with safety and performance requirements, a technical file safeguards public health and facilitates transparent communication with regulators. It is a cornerstone of regulatory compliance and product lifecycle management. The file will also be periodically updated to include post market data, specification changes and customer complaints.
What is Required in a Medical Device Technical File?
Global focus
Each of the major global regulatory bodies, including the U.S. Food and Drug Administration (FDA) and the European Union Medical Device Regulation (EU MDR), establish their own specific requirements for medical device technical files. These requirements are designed to aid medical device designers and manufacturers in proving that their products meet stringent safety and performance standards.
Here is an overview of the major global regulatory bodies involved, and the type of documentation they demand:
FDA Requirements
In the U.S., the FDA mandates a premarket submission, such as a 510(k) – used for medium-risk medical devices (usually Class II), or Pre Market Approval (PMA) – used for high-risk medical devices (Class III), such as devices that are designed to support or sustain human life. Documentation must contain detailed design and development documentation, clinical and non-clinical study results, labelling and quality controls to demonstrate safety and effectiveness.
EU MDR Requirements
In the EU, the MDR calls for a technical file that includes comprehensive documentation on a device’s design and intended use, manufacturing and testing, as well as labelling showing a Unique Device Identification (UDI), a declaration of conformity to confirm the involvement of a Notified Body, as well as a post-market surveillance plan to address potential adverse events effectively.
Main Differences in Global Regulatory Standards
While both FDA and EU MDR emphasise safety and performance, their approaches differ. For instance, the EU focuses heavily on post-market surveillance and clinical evaluation (not necessarily clinical investigation) for all medical device class types, whereas the FDA emphasises premarket approvals. Understanding these differences is critical for global compliance.
If you are interested in medical device approval specific to the UK, read our blog |
To understand the broader landscape of regulations, explore our comprehensive |
UK focus
UK MDR
The UK Medical Device Regulations (UK MDR) 2002, under the MHRA (Medicines and Healthcare products Regulatory Agency), govern the placement of medical devices on the market in the UK following Brexit. These regulations ensure that medical devices meet the necessary safety and performance standards. The UK MDR 2002 shares many similarities with both the EU MDR and the FDA regulations regarding technical file requirements, but there are some distinctions, in particular, UKCA marking.
For medical devices placed on the market in Great Britain, the UKCA (UK Conformity Assessed) marking is required, indicating compliance with the UK’s specific regulatory requirements. While the UKCA marking is similar to the EU CE marking, it is tailored to meet Great Britain specific regulations. (For Northern Ireland, CE marking remains applicable under the Northern Ireland Protocol, and devices must comply with the EU MDR or IVDR requirements.) Manufacturers may also need to undergo conformity assessment procedures, which may involve a UK Approved Body for higher-risk devices.
What is Required in a Medical Device Technical File?
In order to comply and demonstrate a device’s safety and effectiveness, the key components of a medical device technical file must include the following:
- Device Description: Details of the device’s design, intended use and specifications.
- Design and Manufacturing Information: Documentation of design processes and manufacturing methods used.
- Risk Management: Evidence of risk analysis and mitigation strategies.
- Clinical Evaluation: Data proving safety and performance through clinical evidence.
- General Safety and Performance Requirements (GSPR): Evidence of compliance with essential safety and performance standards – required by the EU MDR.
- Quality Management System (QMS) Documentation: Proof of compliance with standards like ISO 13485, covering processes for design, manufacturing and quality control.
- Raw Material Data: Documentation related to the raw materials used, including compliance with BSE/TSE requirements, biocompatibility testing and other additional testing or compliance requirements.
- Labelling and Instructions for Use: Copies of labels, packaging and user instructions
- Sterilisation and Packaging Information: For sterile devices, details on sterilisation processes, validation and packaging are important.
- Post-Market Surveillance Plan: Strategies for monitoring device performance after launch.
Essential Documentation for a Medical Device Technical File
Here, we take a closer look at the key components of a medical device technical file, such as the device description, design and manufacturing information, and clinical evaluation.
Device Description and Specification
Why it’s needed: This section defines the device’s purpose and scope, ensuring it is understood in terms of its functionality, intended users and usage scenarios. It helps regulators assess the device’s overall fit within medical contexts.
Specific info required: A detailed description of the device, including its physical, chemical or biological characteristics. The intended medical purpose, target patient population and any variations (e.g., sizes, configurations) should be included.
Design & Manufacturing Information
Why it’s needed: It helps demonstrate the device was developed using a structured and standardised approach, reducing the risk of defects or unsafe performance.
Specific info required: Documentation of the design phases, materials used, production techniques, specifications, design verification and validation, as well as any design changes. Details of manufacturing processes, including information on equipment and facilities, should be provided to show adherence to quality standards.
For more detailed information on medical device development and its stages, refer to our m |
Risk Management Documentation
Why it’s needed: Risk management ensures that potential hazards are minimised, demonstrating that the device is safe for patient use.
Specific info required: A risk analysis report (often based on ISO 14971) that includes identified hazards, risk assessment procedures, risk control measures implemented and post-market risk surveillance. This may also include a risk-benefit analysis, particularly for higher-risk devices.
Clinical Evidence and Evaluation
Why it’s needed: Clinical evaluation is critical for proving the device performs as intended, ensuring that it does not pose undue risk to users.
Specific info required: Results from clinical trials, clinical investigations or published scientific literature supporting the device’s intended purpose. This includes safety data, clinical outcomes and comparisons to existing devices (if applicable). If applicable, clinical data supporting biocompatibility and long-term effects should be included.
General Safety & Performance Requirements
Why it’s needed: Compliance with General Safety & Performance Requirements (GSPR) is crucial for regulatory approval in the EU market, as it shows that the device meets all necessary health and safety criteria.
Specific info required: A detailed statement outlining how the device meets each of the GSPR criteria for EU MDR requirements. This may include conformity assessments, clinical studies data, performance testing and post market data. Specific references to applicable EU regulations and standards (e.g., ISO standards) should also be included.
Quality Management System Documentation
Why it’s needed: A Quality Management System (QMS) ensures the device is consistently produced and controlled according to predefined quality standards, reducing the likelihood of defects.
Specific info required: Documentation of the manufacturer’s QMS (e.g., ISO 13485 certification) showing how it controls design, manufacturing and testing processes, as well as staff training. Information on supplier controls, internal audits, corrective actions and preventive actions should be included.
Raw Material Data
Why it’s needed: Raw material data is crucial in medical device technical file preparation as it ensures the safety, biocompatibility and regulatory compliance of the materials used. Accurate data on material properties, testing results and safety standards is necessary to meet regulatory requirements, support risk assessments and guarantee the device’s performance and patient safety throughout its lifecycle.
Specific info required: To prove the safety of raw materials in a medical device technical file, the following are typically required:
- Bill of Materials (BOM): A detailed list of all raw materials used in the device
- Raw Material Specifications: Documentation describing the physical, chemical and mechanical properties of the materials
- Biocompatibility Testing: Evidence of testing confirming that the materials are safe for human contact
- Bovine Spongiform Encephalopathy (BSE)/Transmissible Spongiform Encephalopathy (TSE) Compliance: Documentation showing that animal-derived materials are free from prion-related diseases
- Extractables and Leachables (E&L) Testing: Results proving that materials do not release harmful substances when in contact with the body or bodily fluids.
- Chemical Composition and Toxicology Data: Confirmation that raw materials are free from toxic substances such as heavy metals or carcinogens.
- Supplier Certification and Material Traceability: Certificates from suppliers that confirm the materials meet regulatory standards and are traceable for quality control.
Labelling and Instructions for Use
Why it’s needed: Proper labelling and instructions ensure that users understand the correct use of the device, minimising misuse and potential harm.
Specific info required: Copies of all labels, packaging inserts and user instructions. This should include warnings, contraindications, storage conditions, handling guidelines and usage instructions. Additionally, labels should include device-specific details such as batch numbers or expiry dates, as required.
Sterilisation and Packaging Information
Why it’s needed: Ensures that sterile devices remain safe for use, preventing contamination or degradation of the device.
Specific info required: Detailed sterilisation processes, including validation and testing of sterilisation cycles (e.g., steam, radiation or gas). Packaging information should demonstrate the device’s packaging maintains its sterility and protects it during transport and storage. This may include packaging material specifications, test results and packaging design documentation.
Post-Market Surveillance Documentation
Why it’s needed: Post-market surveillance is crucial for identifying and addressing any unforeseen risks that may arise once the device is in widespread use.
Specific info required: A clear plan for ongoing monitoring, including procedures for gathering user feedback, reporting adverse events and analysing trends. It should also detail actions taken in response to any post-market findings, such as recalls or design modifications, and provide a plan for periodic safety reviews.
How to Organise your Medical Device Technical File
For clarity, consistency and faster audits and approvals, follow these tips:
- Structure your documents clearly: Group related sections (e.g., device descriptions, risk assessments, clinical evaluations) together
- Follow a logical order: Start with general device information, followed by compliance and quality documentation
- Keep records up-to-date: Ensure that all information is current and reflects any design changes or updates
- Ensure consistency: Maintain uniformity across all sections to avoid discrepancies
- Label and index: Properly label and index each element for easy reference during reviews and audits.
Common Mistakes to Avoid
When compiling a medical device technical documentation several common mistakes can hinder regulatory approval:
- Missing or incomplete documents can cause delays or rejections, so ensure all required sections, such as risk management and clinical evaluation, are fully documented
- Outdated regulatory information is another critical issue; always check that your file meets the very latest standards and guidelines, particularly for constantly evolving regulations such as EU MDR or FDA requirements
- Documenting changes and updates is essential – failing to keep track of design modifications, testing results or process changes can lead to compliance gaps. Ensuring accuracy, completeness and currency will help prevent costly setbacks.
Keeping your Medical Technical File Up to Date
Maintaining up-to-date medical device technical documentation is essential for regulatory compliance. Regular file reviews and updates should be conducted to ensure that all documentation reflects the latest design changes, testing outcomes and quality control procedures. This helps identify any gaps and ensure accuracy. Additionally, keeping up with regulatory changes is crucial, as standards such as the EU MDR or FDA requirements evolve over time. Stay informed about updates to regulations and industry standards, incorporating any relevant changes into the technical file promptly. By staying proactive, you ensure continuous compliance and reduce the risk of regulatory issues.
Stay prepared for upcoming regulatory changes with resources like Are You Ready for the New Medical Device Regulation?
FAQs About Medical Device Technical Files
Do Medical Device Technical Files Require Certification?
Medical device technical documentation themselves do not require certification, but they must demonstrate compliance with regulatory standards. In regions like the EU, the technical file supports the CE marking process, while in the U.S., it is part of FDA submissions. A Notified Body or regulatory authority audits the file to ensure the device meets safety and performance standards. The device’s manufacturer is responsible for maintaining the technical file and ensuring it meets all legal and regulatory requirements, with certification granted for the device itself.
How Frequently Should Medical Device Technical Files be Reviewed?
Medical Device Technical Files should be reviewed regularly, at least annually, to ensure all information remains current. Reviews are necessary whenever there are design changes, updates to manufacturing processes or revisions to regulatory requirements. Additionally, they should be revisited after any post-market surveillance findings or adverse events. By conducting regular reviews, manufacturers can maintain compliance with evolving regulations, ensure continued device safety and facilitate prompt updates to address any new risks or issues that arise.
*DISCLAIMER: This blog has been written to provide general guidance on Medical Device Technical File requirements. Meridian Medical is not an expert in this field and does not offer technical file preparation services. For expert advice or assistance, please consult a qualified professional. Meridian Medical is not responsible for actions taken based on this content.
Partner with Meridian Medical
If your company is looking for a trusted partner to manufacture high-quality medical devices, Meridian Medical is ready to assist. With a proven track record and a commitment to excellence, Meridian Medical is your ideal contract manufacturing partner.
Contact us today to learn more about our services and how we can help bring your innovative medical devices to market. Get in touch by filling out our online form or contacting us at 01903 732344 or info@meridian-medical.com.
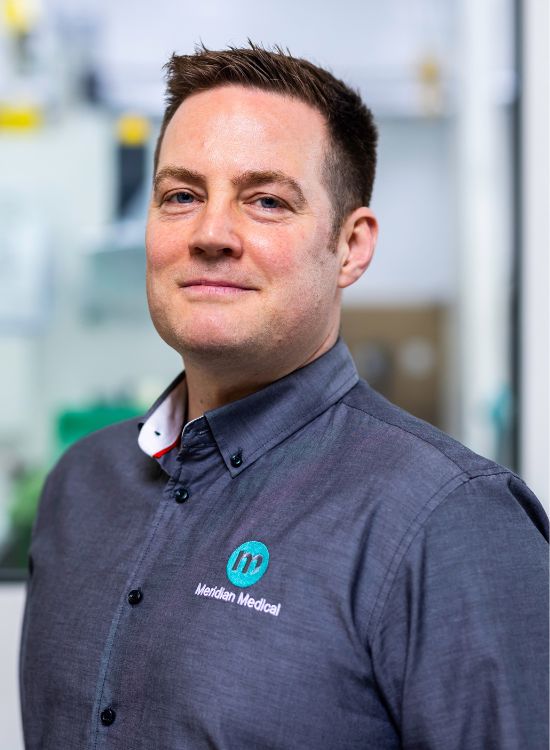
Author: James Fenton, Managing Director
James Fenton, Managing Director of Meridian Medical since 2017, has over 20 years of industry experience. He has been pivotal in developing and producing over 500 types of single-use medical devices, including CE-marked class 2 and 3 devices. With a strong focus on business strategy, project management and customer support, James ensures Meridian Medical's agility and innovation. His expertise is backed by qualifications in Business Studies and Medical Process and Equipment Validation, plus extensive industry training. James's insights into the industry that he has dedicated his entire career to provide a bank of invaluable information aimed at increasing knowledge of and driving advancements in medical device manufacturing.