Cleanroom Medical Injection Moulding
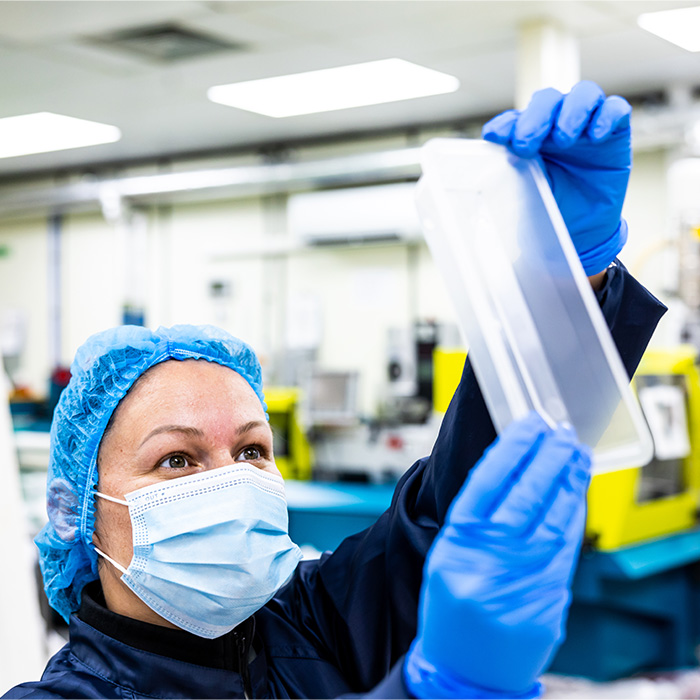
MEDICAL INJECTION MOULDING
Delivering precision, quality, and compliance through dedicated medical injection moulding.
Medical Injection Moulding Services
Injection moulding is a fast, accurate and highly repeatable process used to manufacture plastic components for all types of devices. At Meridian Medical, we combine best-in-class machinery with strict cleanroom protocols and processes to produce components that meet the most demanding Medical and Pharmaceutical clinical and regulatory requirements.
From high-volume part production to sample runs for clinical trials, our injection moulding service is built around the needs of our Medical and Pharmaceutical customers.
Advanced Cleanroom Facilities
All injection moulding operations are carried out in our Class 8 cleanroom, where 12 high-tech machines run 24 hours a day. Our equipment includes:
- BOY 22A (22 Tonne)
- BOY 22E (22 Tonne)
- BOY 22M (22 Tonne)
- BOY 35E (35 Tonne)
- BOY 35E (35 Tonne)
- Engel E-Motion 310/55 (55 Tonne)
- Engel E-Max 310/100 (100 Tonne)
- Engel E-Max 310/100 (100 Tonne)
- Engel E-Max 200/50 (50 Tonne)
- Fanuc Roboshot 130ia (130 Tonne)
- Fanuc Roboshot 130ib (130 Tonne)
- Fanuc Roboshot 220ia (220 Tonne)
Our Fanuc 220ia is also fitted with a six-axis Fanuc M10 robot for high-speed pick, place and machine-tending operations. This set-up ensures efficient, repeatable production in a clean, controlled environment.
The Stages of the Medical Injection Moulding Process
We manage the entire process in-house, from design through to quality-checked components. Here’s how it works:
- Injection mould tool design and prototyping – We work with your CAD files or concepts to design moulds suited to medical applications
- Tool manufacture and validation – Tools are project managed with our approved suppliers, then tested and validated for consistency and accuracy
- Cleanroom production – Medical-grade polymers are injection moulded under strict ISO 13485 protocols, within our class 8 cleanroom.
- Inspection and testing – Parts are inspected using digital measuring equipment to confirm dimensional accuracy
- Packaging and traceability – Cleanroom-ready components are batch-labelled and traceable for full regulatory assurance
Whether you need support at the tooling stage or full-scale production, our team can tailor the service to your project.
Our Medical Injection Moulding typical products
We specialise in producing a wide range of high-quality, medical-grade plastic components through precision medical injection moulding, including:
- Urology and Continence Care – Catheter connectors and balloon tips, Extension line connectors and Urology accessories such as caps, valves, connectors, holders, etc
- Anaesthesia and Infusion – Multi lumen extension set connectors and hubs, custom male and female luer locks, Infusion line connectors and ports and Tubing assembly connectors
- Wound Care and Surgical Devices – Minor surgery kits, involving such items as plastic handles and trays
- Custom Procedure Packs and Surgical Instruments – Surgical plastic hooks, Plastic claw retractors and Instrument trays
- Orthopaedics – Implant centralisers, PEEK implants, and bone cementation accessories.
- Respiratory and Airway Management – Breath and gas analysers, large diameter breathing circuit adapters.
We can work with most medical grade materials such as PP, PC, PVC, ABS, POM, COC, HDPE, PEEK and TPE, as well as specialist polymers for biocompatibility, sterilisation or chemical resistance. Unfortunately we do not offer LSR moulding.
Learn more about our packaging and sterilisation services that follow on from cleanroom production.
Why Use Medical Injection Moulding?
Medical injection moulding offers several advantages in the product development process:
- Consistent quality with tight tolerances
- High repeatability across large production volumes
- Rapid turnaround for both sample and production runs
- Full compliance with medical regulations
If you are producing a medical device, then using a dedicated medical contract manufacturer will reduce any regulatory issues or updates that a conventional ISO9001 moulder will not be aware of. Our moulding validation processes will meet the requirements of MDR, and your time to market will be faster.
Our cleanroom approach ensures the highest standards of consistency and safety in medical device plastic injection moulding.
In-House Expertise and Quality Assurance
Our injection moulding service is supported by a highly skilled in-house team with years of experience in medical device manufacturing. We operate under ISO 13485 and can support both short-run and long-term production.
Digital measuring systems are used to ensure all parts meet defined specifications. Full traceability, documentation and material certification are available for every batch.
Designed for Integration
As part of our full device project management offering, our moulding team works in close collaboration with design, assembly and compliance teams. This integrated model helps avoid delays, streamline approval pathways and bring your medical device to market with confidence.
You can also combine injection moulding with our services for medical device prototyping, assembly and product validation.
Partner with Meridian Medical
- ISO 13485, 9001, and 14001-certified, as well as meeting the requirements of cyber essentials
- Over 30 years of experience in medical plastics
- Cleanroom production with digital QA
- Rapid turnaround and expert support
- Trusted by OEMs and healthcare innovators across the UK and beyond
Ready to get started?
If you need medical injection moulding in the UK with full compliance and cleanroom production, speak to our team today.