Medical Pouch Packaging for Medical Devices
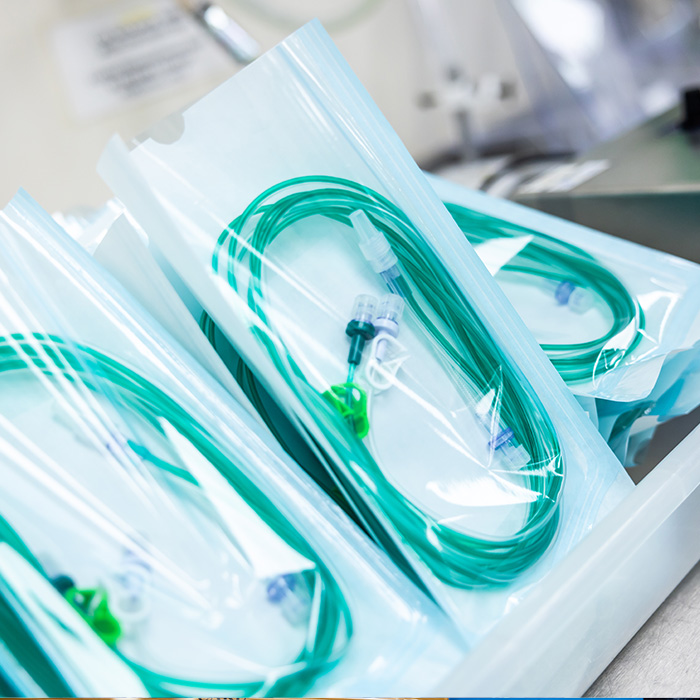
POUCH PACKAGING SERVICES
Meridian Medical specialises in the highest standards of medical pouch packaging, whether it’s needed for a single device or a complex kit of multiple devices.
Pouch packaging for medical devices
Suboptimal pouch packaging for medical devices can compromise the sterility and integrity of even the most precisely engineered products, posing a significant risk to patient safety.
Microbial contamination, including exposure to pathogenic bacteria and other harmful microorganisms, can be life-threatening to immunocompromised or critically ill patients if barrier protection is not properly maintained.
For this reason, medical device pouch packaging – often forming part of a validated sterile barrier system (SBS) – whether in the form of peel pouches or other configurations, must be carried out in full compliance with ISO 11607 and relevant regulatory standards.
Within our ISO Class 7 (Class 10,000) cleanroom environment, a diverse range of medical devices are packaged into high-performance medical device packaging pouches made from validated materials such as Tyvek® and medical-grade paper/poly laminates. Each pouch configuration is selected to ensure optimal compatibility with sterilisation processes and to maintain long-term sterility.
These medical device packaging pouches are used for products manufactured on-site at Meridian Medical, as well as for customer-supplied devices requiring sterile packaging under controlled cleanroom conditions. All pouches can be printed and labelled in accordance with applicable regulatory requirements and traceability protocols.
We are committed to upholding the highest standards of cleanliness, traceability and product integrity, ensuring every packaged device is safe, compliant and ready for clinical use.
How Does Meridian Medical Ensure Quality?
At Meridian Medical, we are committed to maintaining the highest standards of medical pouch packaging quality and compliance. Our processes take place in an ISO Class 7 cleanroom, ensuring a controlled, contamination-free environment.
As an ISO 13485-certified manufacturer, we follow strict quality management procedures to meet regulatory and client-specific requirements. Key industry practices for medical device pouch packaging quality assurance include:
- Verifying material integrity to ensure durability and sterility.
- Conducting seal strength testing to maintain a reliable sterile barrier.
- Ensuring compliance with industry regulations and customer specifications.
Our dedicated Regulatory & Quality Assurance team oversees the entire process, ensuring all packaged products meet the required safety, sterility and performance standards before it reaches the end user, providing peace of mind that the packaging is fully compliant and safe for use.
FAQs
Why Medical Pouch Packaging is Essential for Medical Devices
Medical pouch packaging plays a crucial role in maintaining the sterility and integrity of medical devices from manufacturing to point-of-use. Properly designed sterile barrier packaging protects devices from contamination, moisture and physical damage during storage and transportation, ensuring that they remain safe for use.
Without this level of protection, microbial contamination and exposure to pathogenic bacteria can compromise the device, posing serious risks to patients. This makes high-quality medical device pouch packaging essential for safeguarding patient health.
What materials are used in medical device packaging pouches?
Medical pouch packaging is typically made from validated materials such as Tyvek®, medical-grade paper, polyethylene, polyester and foil laminates. These materials ensure sterility, durability and barrier protection against contaminants, maintaining the integrity of medical devices.
Examples of Medical Device Packaging Pouches
We offer a range of sterile and non-sterile pouch packaging types, including:
- Peel pouches for single-use medical devices
- Tyvek® and paper-based pouches for high-barrier protection
- Custom-designed pouches tailored to specific medical applications
Our expert team works closely with clients to determine the most suitable packaging materials and formats based on device sterility requirements, barrier protection needs and regulatory compliance.