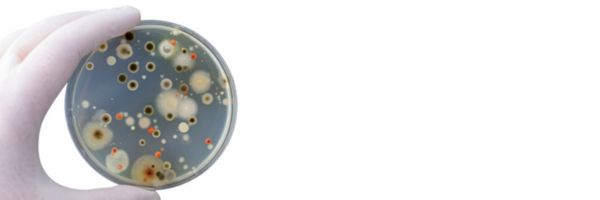
The ability to accurately measure and strictly control bioburden is integral to a high standard of medical device manufacturing and assembly. It is important therefore that your medical device contract manufacturer has systems in place that ensure the lowest possible level of bioburden.
What is bioburden and how is it measured?
Simply put, bioburden is the number of contaminated microorganisms found in a given amount of material before a sterilisation procedure is carried out. Bioburden levels are measured in terms of colony-forming units (CFUs). These units are an estimation of the number of viable bacteria or fungal cells found on a product sample.
A typical bioburden level for a medical device is between 0 and 150 CFUs. The level within this range is dependent on the manufacturing process, the type of material, the size and complexity of the device, and how much handling the product has had during the manufacturing process.
Of course, the bioburden level can be higher than 150 CFUs. If the product sample is particularly contaminated, the bioburden can be classified as “too numerous to count”.
Types of microorganism found during bioburden testing
The types of microorganisms that can be found during bioburden testing are:
- Staphylococci – under a microscope, this microorganism appears spherical and forms in grape-like clusters. It is indicative of human contamination and is a direct result of the handling of a product.
- Micrococci – this microorganism looks the same as staphylococci and forms in the same way. Again, its appearance is an indication of human contamination and is a direct consequence of product handling.
- Bacillus – appears in a rod form under a microscope and is ubiquitous in nature. It is widely found in soil, water, dust and air.
- Yeasts and fungi – these microorganisms appear under a microscope in mushroom-like formations. They are airborne contaminants.
Why does bioburden matter if a device is being sterilised?
When your medical device is being assembled or manufactured, you want it to have the lowest possible level of bioburden, because the lower the bioburden level, the easier it is to sterilise your product.
Each time a gram-negative bacteria is killed, the cells release an endotoxin, which is harmful to humans. This is why it is important that your medical device manufacturing partner maintains the lowest possible bioburden level.
This focus on assuring a low CFU count helps to ensure that any harmful toxins left over from the manufacturing process are removed during the sterilisation process. And the more straightforward the sterilisation process, the more efficient it is, which in turns helps the entire manufacturing process to be more efficient.
Controlling bioburden and your medical device manufacturing partner
In short, to effectively control the bioburden level, your medical device contract manufacturer must control their production areas to a high standard.
Cleanroom control
To reduce airborne contaminants, such as yeasts and fungi, your partner must use a strictly controlled cleanroom for device assembly and manufacturing. All air entering a cleanroom should be passed through high-efficiency particulate air filters. These filters remove airborne particles, in theory down to 0.3 microns in size. To give some perspective, a grain of salt is 60 microns in size, a red blood cell is 8 microns and bacteria are between 1 and 3 microns.
Furthermore, your manufacturing partner should ensure that cleanrooms into which filtered air is passed are kept at a positive pressure. This ensures that any particles that do enter these rooms are pushed out through known gaps or vents.
In addition, your contract manufacturer should be able to clearly demonstrate that they keep their cleanrooms clean. Ideally, they should use isopropyl alcohol solutions on surfaces and equipment to kill surface bacteria brought in by personnel or equipment. They should also ensure that cleanroom staff wear hair nets, gowns, masks and gloves to reduce particulate shedding. You should also check that they have protocols in place to avoid the overhandling of products and to ensure that products are covered whenever possible.
Cleanroom testing
When choosing your medical device contract manufacturer, you should check that their production areas are regularly tested, both internally and externally, to ensure that high standards of control are maintained. Your manufacturing partner should use settle and contact plates to capture surface and air particles, enabling them to confirm whether their procedures are working and being followed and, if required, to quickly address any issues.
Meridian Medical is an established and experienced contract medical equipment manufacturer specialising in a wide range of medical device design, development and supply services.
To find out more about how Meridian Medical can help you with your medical product design and manufacture, get in touch today by filling out our online form or contacting us on 01903 732344 or info@meridian-medical.com.
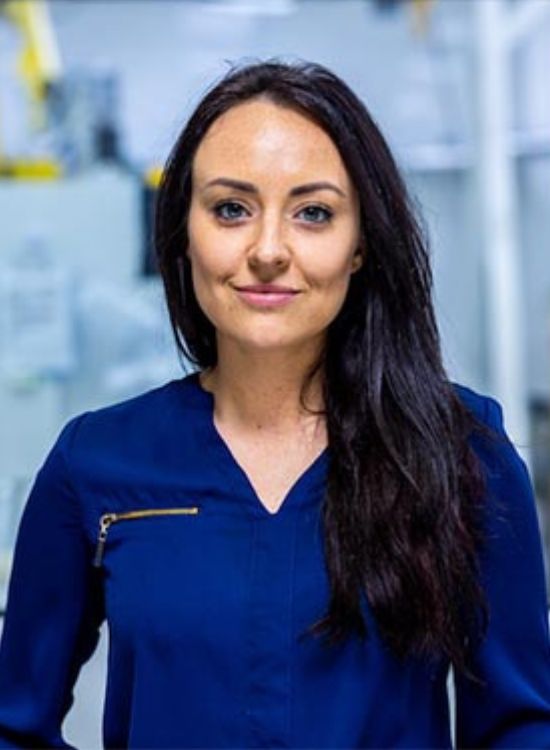
Author: Fiona Chitty, Quality and Process Engineer
Fiona Chitty brings a fresh perspective to Meridian Medical, where she has spent the past four years honing her expertise in quality and process engineering. With a Bachelor of Science in Physics and a Bachelor of Engineering in Chemical Engineering, Fiona is deeply involved in root cause investigations, complaint resolution, trend analysis, and continuous process improvement. Her role is critical in maintaining high standards across all departments, ensuring the delivery of top-quality medical devices. Fiona’s passion for problem-solving and her analytical approach make her an invaluable asset to the team.