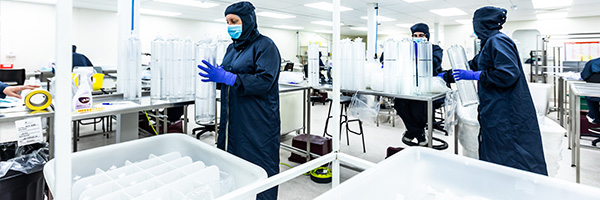
When choosing a contract medical device manufacturer, one of the most important criteria on which to base your decision is the standard and scale of medical cleanroom assembly facilities.
Cleanrooms are a vital part of the medical device manufacturing process – the assembly of many medical products has to take place in them. Cleanroom assembly reduces the risk of elevated microbiological contamination, helps ensure the safety of your products and protects hospital staff and patients.
To help you make the right choice of specialist medical device contract manufacturer, and to help ensure the quality and success of your medical products, we have put together this brief guide to what to look for in a medical cleanroom assembly partner.
How to assess medical cleanroom assembly facilities
When you are selecting your dedicated medical device contract manufacturer, you should use the following criteria to assess their medical cleanroom assembly facilities.
- In-house facilities and expertise. The use of in-house facilities and expertise are preferable to the outsourcing of services by your contract medical device manufacturing partner. This helps ensure consistent quality standards throughout the product assembly process, while generating cost savings and reducing lead times.
- Regulatory compliance. Your partner’s medical cleanroom assembly facilities must be compliant with all the relevant standards. There are a number of regulations that govern the operation of medical cleanrooms. ISO 14644 family details all the requirements such as design, cleaning, test methods, and ongoing performance monitoring.
- Flexibility and scale. Different medical devices have different cleanroom assembly requirements. As such, it is important to choose a contract medical device manufacturer that has the size and range of operations to manage all of your medical product assembly needs. The ability to offer flexibility without sacrificing quality or compliance is critical.
- Capacity and function. It is important that your medical device assembly partner operates cleanrooms dedicated to different functions (for example, Class 7 and Class 8 cleanrooms for the injection moulding, assembly, manufacturing and packaging of sterile and non-sterile medical devices). Each cleanroom must be operated to the relevant standards, such as those relating to air flow, masking requirements, electric machine use and packaging activity.
- Inspection and testing. It is critical that your medical cleanroom assembly partner regularly inspects and validates their cleanrooms to ensure that the appropriate levels of cleanliness are rigorously maintained and relevant project and industry standards are always meet.
- Proven track record. You want a contract medical device manufacturer that you can trust – a specialist that consistently performs to high standards and will ensure that your products are of the highest quality. Look out for testimonials and case studies that give an indicator of this level of expertise and experience.
There are many factors to consider when outsourcing your medical device manufacturing. One of the most important is the standard of medical cleanrooms that a potential partner operates. This has a direct impact on the safety, performance and success of your products.
So, when you are assessing prospective partners, make sure the full-service specialist medical device contract manufacturer that you choose has a comprehensive medical cleanroom assembly facility offering.
Meridian Medical is an established and experienced contract medical equipment manufacturer, specialising in a wide range of medical device design, development and supply services.
To find out more about how Meridian Medical can help you with your medical product design and manufacture and the cleanroom assembly cost factors, get in touch today by filling out our online form or contacting us on 01903 732344 or info@meridian-medical.com.
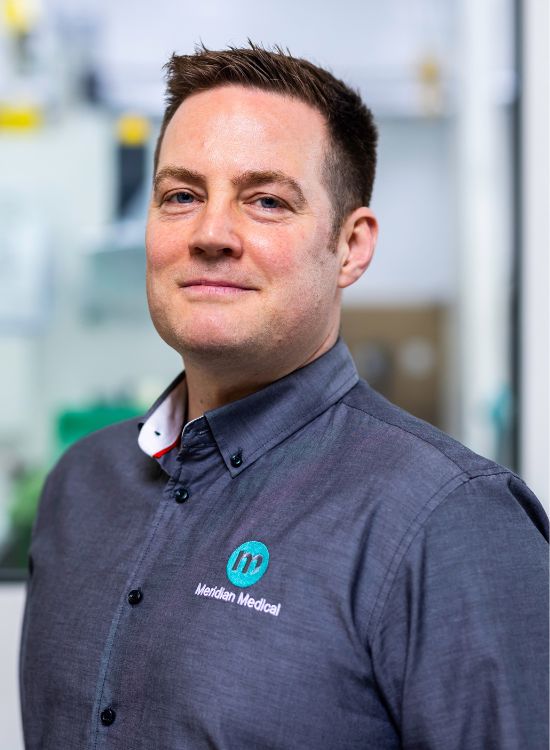
Author: James Fenton, Managing Director
James Fenton, Managing Director of Meridian Medical since 2017, has over 20 years of industry experience. He has been pivotal in developing and producing over 500 types of single-use medical devices, including CE-marked class 2 and 3 devices. With a strong focus on business strategy, project management and customer support, James ensures Meridian Medical's agility and innovation. His expertise is backed by qualifications in Business Studies and Medical Process and Equipment Validation, plus extensive industry training. James's insights into the industry that he has dedicated his entire career to provide a bank of invaluable information aimed at increasing knowledge of and driving advancements in medical device manufacturing.